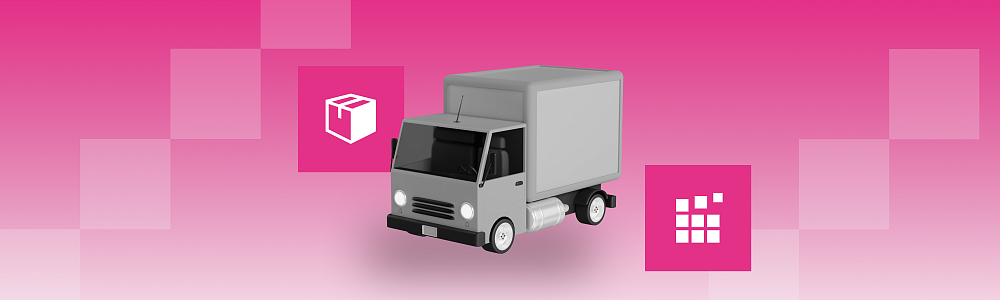
This article will provide techniques and solutions to help protect your business from these negative impacts. Also, we will discuss how Enterprise Resource Planning (ERP) systems can be a useful tool which streamlines inventory management, reduces risks, and improves efficiency in the inventory management process.
What is Inventory Management?
The goal is to maintain an ideal inventory level that is enough to meet customer demand without overstocking. By doing this well, a company can avoid waste,save money and ensure products are readily available for customers.
How Inventory Management Works
Let's use a construction company as an example to understand the workflow.
1. Planning and Forecasting
Planning helps identify the type and quantity of inventory, including steel, concrete, tools, and machinery, required for upcoming projects to prevent project delays. Forecasting lets you keep just the right amount of stock: not too much so you lose money, and not too little so you miss out on sales.
2. Purchasing and Receiving
Upon receiving, the team inspects the materials for quality and quantity to ensure they match the purchase orders. This process ensures stock levels remain accurate and that the right products are available for or use.
3. Storage and Warehousing
The company uses inventory management software to catalog and track the location and status (e.g., assigned, reserved, in-use) of each item. To keep losses low and ensure materials are always available, it's important to organize them well and protect them from theft and damage.
This gives you a constant, real-time view of what’s in stock. Use technologies such as barcoding and RFID tags to make this process more efficient; these tools update your inventory levels automatically, eliminating manual errors. With precise knowledge of your inventory at any time, you have the capability to make informed decisions on when to reorder, which ensures the availability of popular items.
4. Reordering
For example, review your sales records from the past year and note the duration required for new stock to arrive. This process allows you to set these reorder points accurately.
Such a proactive strategy guarantees the maintenance of sufficient stock to meet anticipated customer demand without the risk of overstocking.
5. Order Fulfillment and Shipping
The logistics team organizes the transportation of these items from the warehouse to the construction sites, ensuring they arrive in the needed time frame to keep the project on schedule. This might involve coordinating with various transportation providers and handling the necessary permits for large machinery or hazardous materials.
6. Controlling and Reviewing
The review process helps identify inefficiencies and implement improvements in procurement, storage, and logistics. It saves money by avoiding too much or too little stock and ensures customers get what they want fast.
Core Benefits of Inventory Management
Techniques for a Better Inventory Management Strategy
Find the inventory management strategy that best matches your company's needs by exploring our overview of the popular strategies.
1. Perpetual Inventory System
For example, if your construction project uses a perpetual inventory system, each time a worker takes out materials like timber or screws, the system automatically updates the inventory count. This real-time tracking means you always know exactly what you have on hand, which helps prevent stockouts and overstocking. It also permits more accurate plans and reorders, ensuring your project advances smoothly.
2. Safety Stock
Imagine your project is in a remote location where delivery times are unpredictable. You should keep a safety stock of essential items like cement or bricks to ensure that even if there’s a delay in your supply chain, your project can continue without interruption. The amount of safety stock you maintain should be based on the variability of demand and lead times for replenishment.
3. Vendor-Managed Inventory
VMI means your supplier keeps an eye on your stock for you. When it's low, they send more without you having to ask. This makes the workflow easier for you, keeps your supplies coming, and lets you pay attention to other project tasks.
4. Economic Order Quantity (EOQ)
Imagine you need to order cement regularly for your construction project. If you order too much at once, you’ll incur high holding costs as you pay for storage. If you order too little, you’ll face frequent ordering costs and potential delays. EOQ helps you calculate the optimal order size, balancing these two costs. This ensures you order the right amount of materials at the right time and avoid excess inventory and stockouts.
5. Batch Tracking
In a construction project, if you receive concrete in batches, batch tracking would involve tagging each batch with a specific identifier. If there’s a problem with the quality of concrete in a particular section of your project, batch tracking allows you to quickly identify which batch was used and trace it back to the supplier or production process. This method is invaluable for maintaining quality standards and managing recalls or quality issues effectively.
The Inventory Management module of FirstBit ERP allows for efficient batch management of your stock, enabling seamless processing of order batches. This feature offers enhanced control over inventory quality and facilitates precise tracking.
6. ABC Analysis
For example, in a construction project, “A” items include high-cost items like heavy machinery or specialized materials that are critical to the project. “B” items can be more common but still essential materials like standard tools. “C” items are everyday consumables like nails or screws. By focusing more on managing “A” items, such as by keeping them under close supervision and ensuring timely reordering, you can ensure that the most critical aspects of your inventory are always well-managed, while less effort is spent on lower-value items.
7. First-In, First-Out (FIFO)
In the context of construction, consider materials like paint or adhesives that may have a shelf life. Using FIFO ensures that users consume materials in the sequence they arrived, which reduces the risk of waste due to expiration. For example, if you receive a batch of paint in January and another in March, FIFO dictates that the January batch should be used up before you start on the March batch, ensuring that older stock is always used first.
FirstBit ERP has a FIFO inventory management approach, ensuring that older stock is used or sold before newer items, thereby reducing the risk of inventory obsolescence and waste.
8. Just-In-Time (JIT) Inventory
For instance, if you’re managing a construction site that requires steel beams, using JIT means you would coordinate with your supplier to deliver the steel only when the project reaches the stage where it’s needed. This way, you avoid having large quantities of steel sitting idle on-site, reducing storage costs and the risk of damage. JIT requires close collaboration with suppliers and precise planning but can significantly improve efficiency and reduce waste.
Integration of KPIs
Overcoming Challenges
1. Inconsistent Tracking Across Channels and Locations
Implementing an integrated system that syncs inventory data in real-time across all channels and locations can mitigate this challenge, ensuring that stock levels are accurately reported and managed.
Solution: By choosing to integrate a construction ERP system with an inventory module, you directly tackle the problem of inconsistent tracking across different locations and channels. This solution offers you a bird's eye view of your in real-time. This means no more guessing about stock levels or whereabouts.
Whether you're dealing with materials at a job site or products in different warehouses, you'll have up-to-date information at your fingertips. This visibility helps in making informed sales and replenishment decisions, reducing the risk of stockouts or overstocking.
2. Inaccuracies in Inventory Data
Solution: The challenge of inaccurate inventory data affects customer satisfaction and order fulfillment rates. By implementing ERP solutions that automate data collection using barcode scanning and RFID technologies, you minimize human errors.
These technologies capture and update your inventory data accurately and quickly. This ensures that orders are fulfilled correctly, improving customer satisfaction and trust in your services.
3. Fluctuating Market Demands
Solution: Fluctuating market demands leading to overstocking or stockouts can be navigated with an inventory management ERP software equipped with forecasting tools. Predictive analytics, machine learning algorithms, and historical data analysis enable you to anticipate future sales trends.
By understanding what your customers are likely to buy in the future, you can adjust your stock levels accordingly, preventing the wastefulness of overstock and the missed opportunities of stockouts.
4. Inefficiencies in Manual Documentation
Solution: Manual documentation not only slows down operations but is also prone to errors, which can escalate as your business grows. Implementing an ERP system that digitizes and automates documentation processes reduces these manual errors significantly. It keeps your operations running smoothly and efficiently, scaling up as your business grows without adding extra burden or increasing the risk of mistakes.
5. Complex Supply Chain Challenges
Solution: Dealing with a complex supply chain becomes much more manageable with modern ERP systems that include a supply chain management module. This solution provides visibility and control over your entire supply chain, facilitating efficient communication with suppliers and making logistics planning more straightforward. It addresses inefficiencies and potential disruptions by allowing you to proactively manage relationships and logistics operations, ensuring timely and consistent product delivery.
6. Excessive Inventory and Storage Issues
Solution: The problem of excessive inventory clogging up storage space and tying up capital can be solved with software that includes tools for maintaining optimal stock levels. This software helps you accurately predict demand based on various data, allowing you to order just enough inventory to meet your needs without overdoing it. This not only keeps your operations running smoothly but also minimizes the risk of having unsold stock that can become outdated or spoil, saving you money and space.
One reason your inventory management is not sufficient can be inadequate software as well. To address that, you can adopt an integrated, cloud-based inventory management platform and leverage vendor expertise and training services at implementation.
Tackle Inventory Management Hurdles with the FirstBit ERP System
Storage and Purchasing
You can specify the item storage parameters and replenishing parameters.
Batch management
Negative Stock Management
With FirstBit ERP, you can enhance the accuracy of the cost of goods sold by avoiding the issue of negative inventory by analyzing the order and shipping dates.
Serial Numbers Management
Track the complete history of each serial number. Supplier details, Customs information, Sales, Exchange, and Return transactions.
of your processes and scale your business with FirstBit ERP now!